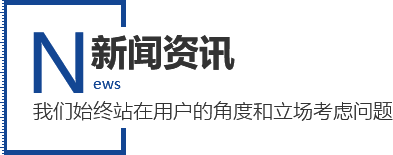
工程陶瓷材料具有高硬度、高耐磨性、抗腐蚀性和耐高温等物理和机械性能,已广泛应用于航空航天装备等领域。
工程陶瓷制品加工工序复杂,每道工序都可能形成影响性能的缺陷, 因此,有必要采用高灵敏度的测试手段对陶瓷材料微缺陷进行全方面检测。
无损检测(NDT)在不改变被检对象使用性能的前提下评价材料完整性和连续性,检出固有缺陷及其形状、位置和大小等信息,适于检测加工效率而成本高的工程陶瓷材料的缺陷情况。
陶瓷材料常规无损检测方法
▍液体渗透检测技术(PT)
液体渗透检测利用液体毛管作用原理,能够对多种材料及其制件表面开口缺陷进行非破坏性检查。可检测出非多孔性、固相材料开口于表面之间断。
对均匀而致密的工程陶瓷材料,荧光或着色渗透方法能检出开度小至1μm的气孔、裂纹等表面缺陷,但对料表面粗糙度和整洁度要求高,未经预清洗或沾有污物的表面和空隙会产生附加背景,影响识别检测结果。
渗透检测的基本原理:渗透检测是基本与液体的毛细作用(或毛细现象)和固体染料在一定条件下的发光现象。
渗透检测的工作原理:渗透剂在毛细管作用下,渗入表面开口缺陷内;在b除工件表面多余的渗透剂后,通过显象剂的毛细管作用将缺陷内的渗透剂吸附到工件表面形成痕迹而显示缺陷的存在。
▍超声检测技术(UT)
超声检测利用超声波在弹性介质中传播,在界面产生反射、折射等特性来探测材料内部或表面/亚表面缺陷。
目前,国外开始将人工智能、激光技术、数字信号处理、神经网络以及断裂力学知识与超声检测相结合,对陶瓷制品的强度和剩余寿命进行评估。
超声波工作的原理:主要是基于超声波在试件中的传播特性。
a.声源产生超声波,采用一定的方式使超声波进入试件;
b.超声波在试件中传播并与试件材料以及其中的缺陷相互作用,使其传播方向或特征被改变;
c.改变后的超声波通过检测设备被接收,并可对其进行处理和分析;
d.根据接收的超声波的特征,评估试件本身及其内部是否存在缺陷及缺陷的特性。
超声波技术在工程陶瓷材料无损检测中的应用:
▍微焦点射线检测技术
常规工业X射线设备焦点尺寸为1~ 4 mm,0. 2~ 0.5 mm被称做小焦点,工业微焦点范围为0. 05~0.001 mm。相对于:规射线照相设备,微焦点X射线成像系统对缺陷的识别能力更高。
传统射线照相和微焦点成像的比较
因为X射线源的大焦点、胶片颗粒度或荧光屏的杂斑等会导致图像清晰度和对比度下降,限制了所得到的信息量。而微焦点技术可通过图像投影放大获得更多的图像细节。
微焦点X射线法能检出陶瓷材料内部小至10μm的裂纹,但裂纹延展方向应与射线束方向一致。
▍激光超声检测技术
利用激光产生超声波的方法可分为直接式和间接式两大类。直接式是使激光与被测材料直接作用,通过热弹性效应或烧蚀作用等激发出超声波;间接式则是利用被测材料周围的其它物质作为中介来产生超声波。
激光超声以非接触式激光干涉仪接收超声波,能够远距离遥控操作并抗干扰性,可饺芳觳夤こ烫沾刹牧媳砻嫒毕菸恢煤统叽纾阅诓苛盐萍翱籽ㄓ薪虾玫募觳庑ЧⅫ/p>
红外检测(infrared testing)基于热辐射的普朗克定律,扫描工件外表面由于缺陷引起的温度差异,从而测定表面或内部缺陷位置。
工程陶瓷材料需要经过高温烧结才能变得致密坚硬,红外检测技术能在粉体烧结阶段对陶瓷质量进行控制和分级筛选。在陶瓷无损检测中利用红外技术与扫描成像系统结合,可对氮化硅透平叶片进行缺陷检查,发现表面约100μm的细小裂纹。
红外热波检测技术具有快速检测陶瓷材料面积型缺陷的潜力,检出微缺陷成功率高,应用前景十分广阔,但今后还需解决工件表面、背景辐射及缺陷大小和深度对检测灵敏度影响的问题,相应的温度记录曲线的解释须借助专业知识。
▍声发射检测技术
声发射检测(acoustic emission testing)通过接收陶瓷受应力时工件内部裂纹形成和生长发出的声信号判断声发射源的位置信息和实时活动情况,主要用于在线监测陶瓷材料内部缺陷动态扩展过程,进行陶瓷寿命预测和质量评估。
与金属材料不同,陶瓷材料运用声发射检测需要考虑声信号的衰减,尤其是不同方向的声发射信号衰减和声速变化规律。材料缺陷大小会影响声发射信号强弱,环境和检测设备的噪声也会对传感器产生干扰,解决好这些问题便能为声发射检测带来更好的发展。
▍工业CT技术(ICT)
工业CT利用高能射线扫描工件得到断层投影数据,经图像重建算法重建出断层图像、
工业CT优势:
空间和密度分辨率小于0.5%
成像尺寸精度高
不受工件材料种类和几何形状限制
可生成材料缺陷的三维图像
(资料来源于网络-百度搜索)