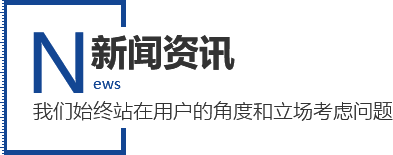
从近几年新材料在汽车行业的应用研究可以看出,国内外主要汽车厂商在材料的使用上主要分为三个方面,分别是:使用轻质合金作为汽车零部件材料;在汽车车身中使用高强度钢;使用碳纤维以及热塑性材料等新材料。科技的发展带来了质量更轻、更坚固的新型材料,这些材料被广泛的应用于汽车当中,既保障了汽车的安全性,也降低了车身的质量,而且节约成本。
轻质合金在汽车行业的应用进展
1 镁合金材料在汽车行业的应用进展
目前各大汽车厂商所使用的镁合金可分为AZ系列、AM系列、AS系统以及AE系列。现如今的镁合金在汽车中的应用主要是针对零部件的壳体,使镁合金所构成的零部件能够耐温达到200℃左右,不过目前所生产的镁合金还远未达到这一高度,而能够达到这一要求的稀土合金往往价格较高,很难应用到汽车中,因此,由镁-稀土所构成的合金成为当今应用的主流产品。
现如今国内外对镁合金的研究成果十分丰富。早在2006年时,德国戴姆勒-克莱斯勒公司就推出了一辆由镁合金构成车顶的概念车,在这辆车中大量的使用镁合金从而使其质量比同级别车降低20%,这一概念车的推出有效的证明了汽车的减重与安全性保障是可以同时保证的。
在近这十年时间内,汽车行业对镁合金的使用情况飞速提升,每年的增速都是10%左右,这些镁材料主要应用在汽车中的零部件与内饰部分,在今后的十年内,镁材料在汽车行业中的应用会继续保持10%左右的增长速度。在今后的发展应用中,镁合金应当向合金的优化、减轻腐蚀、创新生产工艺等方向发展,以达到汽车中更多零部件都能够使用的目的。
2 铝合金材料在汽车行业的应用进展
铝合金材料在汽车行业中的应用,其主要的优势有5点:其一,使用铝合金材料的新型车整车比使用传统材料的整车质量能降低三到四成;其二,整车安全性更高,具有较高的安全系数;其三,和同级别采用传统材料的汽车相比,能耗减少一半左右;其四,铝合金材料能够被重新利用,有效的节约了资源浪费;
铝合金自身具有很多的优点,比如密度小、比强度和比刚度高、弹性好、抗冲击性能良好、耐腐蚀、耐磨、高导电、高导热、易表面着色、良好的加工成型性以及高的回收再生性等。这些优点使得铝合金材料被业内一致认为是“希望金属”。
随着铝合金材料在汽车车身的应用越来越广泛,在今后的发展过程中,应当努力提高创新能力,在降低铝成本的同时提高生产效率。比如在汽车车身方面,由于车身线形较多,十分复杂,再加上车身所需要承受的阻力较大,所以在应用铝合金材料时,对铝合金材料的要求较高,这也是今后铝合金材料发展的重要方向之一。
高强度钢在汽车行业的应用进展
镁、铝合金在汽车行业中的应用主要集中在汽车的零部件上,不过这两种材料在成本与工艺方面的使用有一定的劣势,不利于在汽车上的大范围使用。而随着高强度钢的面世,其所具有的高抗碰撞能力与质量轻于铝、镁合金等特性使其在汽车行业得到了快速的应用。这种新型材料一方面能够显著降低汽车车身的整体质量;另一方面又可以提升整体车身的安全性。因此,现阶段高强度钢也是汽车行业轻量化发展中的一种重要材料。
目前,主要的轻质高强度的钢铁材料主要有:高强度钢(屈服强度大于2MPa)、超高强度钢(屈服强度大于550MPa)和高强度钢(以下统称为高强度钢)。高强度钢取代普通钢材用于车身零件和其他结构件取得了良好的减重效果,大多<轿车的保险杠、骨架、前门、后门横梁等都采用高强度钢作为材料。而且,高强度钢在车辆零部件方面的使用比例在逐渐增加,应用比例已由1997年的7%上升到现在的50%,预计今后几年还会有提升。
但是高强度钢应用的技术难点在于成形技术。目前高强度钢成型的主要问题是与弹性应力及应力释放相关的零件尺寸精度和回弹问题。具体来讲高强度钢在成形过程中的主要问题是:(1)变形过程中出现加工硬化,屈服强度提高,流变应力较高;(2)由于零件厚度减小,因而不易保持原状等问题。
汽车用高强度钢的另一种发展思路是保留钢材本身的优点,即强度、韧性、可加工性、寿命等前提下降低钢质量密度。其中一种方法是向钢中添加诸如Al、Si等轻金属合金元素。这些钢已在早期开发出来,具有较高的强度、较低的密度以及经过改善的耐蚀性,从目前来看其发展潜力很大。近,钢基复合材料也被提出同时用于提高杨氏模量(E)和降低产品密度(ρ)。由于增强颗粒的参数(性质、体积分数、尺寸等)的选择余地增加,所以E/ρ比率能够得到显著提高,而且材料的延伸性和耐破损、耐疲劳性也与常规的超高强度钢处于同一水平。因而,汽车用高强度钢发展前景广阔,同时对汽车新材料发展具有强大的推动力。
碳纤维材料在汽车行业的应用进展
碳纤维主要是含碳量在90%以上的高强度、高模量纤维,具有一般碳素材料的特性,如耐高温、耐摩擦、导电、导热及耐腐蚀等特点。这种新型材料具有较小的比重,外柔内刚,与铝材料相比在质量上有明显的优势,同时碳纤维在抗拉弹性、抗腐蚀性n方面也十分优异,可以被看作是新一代的加强版纤维材料。
就目前学者对碳纤维的研究来看,碳纤维的制作仅能够从碳或者是石墨中提取,而其本质特性还没有被完全研究出来。现阶段汽车中使用的碳纤维主要存在于传动轴、刹车片等部件。当今汽车整体车身基本上都是由钢铁所构成,如果汽车中的钢铁材料都能够换成碳纤维,那么汽车的车身质量能够减轻300kg左右,能耗降低、整体汽车效率提升,CO2排放量也能够得到明显的控制。因此,碳纤维在汽车行业中的应用是汽车行业今后发展的一个重要方向。
碳纤维复合材料制成的传动轴质量轻、具有很好的耐疲劳性、耐腐蚀性,而且震动衰退性好、安全性强。金属传动轴质量重而且易磨损,磨损后又会引起传动噪音和能量损失,缩短了传动轴的使用寿命。碳纤维复合材料满足结构件性 要求时可比钢材传动轴减重70%~80%,而且强度和使用寿命增加许多。因此,选用碳纤维复合材料生产传动轴具有重要意义。碳纤维复合材料传动轴根据形式可分为整体型和装配型两类。
在石油危机暴发后,国际上对于节能减排问题的研究已经越来越重视,也成为全球汽车厂商所共同追求的方向。要想解决这一问题,较为重要的是一个努力方向便是对新材料进行研究,并将这一新材料应用在汽车中。碳纤维由于自身所具有的多种优点被越来越多的汽车厂商所认可,已经成为有希望解决目势敌幸邓媪俚奈侍獾耐揪丁O秩缃瘢枷宋诖笮偷纳逃梅苫1赛车等方面已经得到了应用与认可,已经被充分证明了,该材料能够替代钢铁等传统材料,只是该新型材料性质属于复合型材料,在应用时需要经过大量的计算与数据的积累。
热塑性材料在汽车行业的应用进展
随着科学技术的不断发展,汽车行业所使用的材料也向着更加轻量化、更加安全的方面不断发展。热塑性材料便是二十一世纪汽车行业发展的重要材料之一。就目前汽车行业的发展情况来看,热塑性材料主要应用集中在汽车的内饰与密封系统。
热塑性材料在汽车内饰的应用进展。传统汽车内饰所使用的材料多为注塑成型、表层热成型等类型,这些材料无论是在触感、质量与环保方面都存在一定的问题。而热塑性材料在汽车内饰中的应用能够显著降低成本,效率高,促进汽车整体生态圈的运转速度,为企业创造更大的价值。
热塑性材料广泛应用于汽车密封条方面。市场对于汽车密封条,尤其是轿车密封条的性能要求愈来愈高,不仅需要具有优良的密封性,而且要美观环保。在这些需求的推动下,汽车密封条技术不断推陈出新,热塑性材料中的热塑性硫化橡胶(TPV)得到了广泛的应用。该材料得到广泛应用的首要原因是环保的要求,传统的材料在使用中产生致癌亚硝酸的促进剂(BZ、TT等),而TPV不存在上述环保问题。2017年起所有的国产及进口汽车可回收利用率要达到95%,在材料回收利用方面TPV具有很大优势。此外,TPV无需混炼和硫化,可以与硬质塑料(PE、PP)共混挤出生产彩色蕴酰蚒V性能强,而且接角可以热熔炼。
热塑性材料能够显著的提升其加工性能并且能够保障玻璃密封具有持久性与抗老化性,提升了玻璃的使用年限。
总结
汽车行业的快速发展不仅给我国社会生产等方面带来便捷,而且也带来了诸多问题,面对这些问题,应当以科学的方式对待,好的解决办法便是研制出质量更轻、强度更强、更加环保的材料来代替传统的钢铁材料,这样就能够有效的<轻车身质量,达到节能减排的效果。
(资料来源于网络-中国腐蚀与防护网)