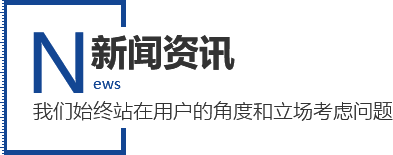
在一些受监管的消费行业中,无论是单一组件、材料还是主要组件和装配体,对其进行合适的测试都是至关重要的。虽然汽车行业对于材料和部件的测试有着特殊要求,但疲劳原理在汽车领域内甚至是整个工业领域内都是通用的。
材料的疲劳是指在循环加载下,发生在材料某点处局部的、永久性的损伤递增过程。经足够的应力或应变循环后,损伤累积可使材料产生裂纹,或使裂纹进一步扩展至完全断裂,出现这些可见裂纹或者完全断裂都叫疲劳破坏。
John Tartaglia博士解释道:“通常情况下,我们将破坏循环次数在100至10000次之间的疲劳称之为低周循环疲劳(LCF),这类循环作用于零件、构件的应力水平较高。对于破坏循环次数高于10000次的称之为高周循环疲劳(HCF),作用于零件或构件的应力水平较低。考虑到汽车上的许多组件可能需要经历上百万次的循环,因此了解这些是非常有必要的。”
为了进一步了解疲劳试验在现代汽车行业内的应用现状,Quality杂志与Tartaglia博士、Alex Johnson工程师以及Steve Panter工程师进行了许多的交流讨论,以下是其中讨论的一部分。
QUALITY:在汽车行业里,哪些材料和部件通常需要进行疲劳试验?
JOHN TARTAGLIA:在材料方面,汽车行业内主要采用钢材料作为主体结构部分、铸铝用于缸体和缸盖、铸铁用于曲轴等方面。铝材料现在越来越多的被引用到汽车车身板件和结构件中;钢铁材料则正逐渐以新的形式应用,例如,利用液压成形技术制造管形零件p减少材料的重量(与传统的实心棒材和板状结构相比)。
我们可以将材料在汽车内的使用分为车辆的结构部件和动力系统两方面。汽车的结构部分包括用于门和踏板的中心柱、车身框架,保险杠,支架,发动机支架,座椅部件,座椅靠背和车轮等,所有这些部件都要从振动的角度出发对其进行疲劳测试。由于测试费用和复杂性的原因,车头和车身并不经常进行疲劳试验,大多数情况都是从这些部位上切除一些样品进行测试。但是,曲轴和整个发动机仍然需要在高温以及高负载条件下进行相关实验。
QUALITY:对不同的材料进行疲劳试验是否会有所差异,例如复合材料和金属材料?
JOHN TARTAGLIA:在汽车制造业,通常会用到聚合物基复合材料(PMC)和碳&维增强高分子复合材料(CFRP);与金属材料相比,这些材料的疲劳试验确实有所差异。从测试装置角度来看,这些复合材料的疲劳试验需要的加工技术以避免其中纤维材料的拔出、灵敏的测力传感器以测量低载荷应力、固定夹紧装置以防止样品断裂(对于金属材料则是不必要&)。
此外,由于具有各向异性的特性,聚合物基复合材料的疲劳试验还有另一个难处。这种各向异性使得材料的性质会随着测试方向的不同而发生改变,因此还需要采用一些技术去除掉这种各向异性。总之,在对这些材料进行疲劳试验时需要考虑到载荷加载方向的影响。
是否存在某些程序和考虑因素使得汽车行业的疲劳测试与其他行业有所区分,例如航空航天领域?
STEVEPANTER: 测试差异主要包括加载应力大小、加载轴要求、环境条件、测试方法和文档要求等方面。此外,取决于系统应用/要求,有时候还需要考虑到最终用户的使用环境等因素。
ALEX JOHNSON: 为了防止一些灾难性的事故,汽车行业非常注重材料的碰撞性能和冲击性能。其他一些行业则可能更加注重材料在正常条件下的使用寿命,而汽车行业重点关注的是产品的质量安全问题。无论是消费者的私家车辆、商用车辆还是高性能的竞赛型车辆,都需要具备能够在受到撞击时保护乘客的功能。
疲劳性能测试能够使汽车制造商们更好的了解他们产品的生命周期,反过来这也有助于延长产品的保修期限,提高产品的市场竞争力。现在,电动汽车的开发促使汽车制造商们研究电池和轻质材料的使用以提高汽车的使用效率和减少碳排放量。但是新的部件和材料必须进行耐久性测试,以确保它们可以用于优化性能,同时保持安全性。
疲劳试验在过去20年有什么变化?
JOHNSON: 在一些安全至上的行业和应用方面,了解材料的使用寿命是产品设计和开发过程中非常重要的一部分。随着现在对更高燃料效率以及材料和结构的轻量化的持续追求,正驱使着研究人员在不牺牲产品安全性能的前提下尽可能挖掘材料的使用潜力,甚至接近于材料性能极限。现在材料领域的进步加上制造技术的发展,导致疲劳测试显得更为重要。在大规模生产应用中更广泛地使用复合材料就是一个很好的例子。
当你看到风力涡轮机的叶片沿其长度使用数百种不同的复合材料时,你就会明白对于材料结构进行优化以使其适用于特定环境是多么的重要。随着现在金属烧结技术和3D打印技术的使用日益广泛,我们在金属材料身上也看到了类似的趋势,研究人员正对这些材料根据具体的应用进行优化。
未来材料技术、加工方法或者工具的发展是否会引起疲劳试验发生变化?
TARTAGLIA: 虽然在过去的五十年里疲劳试验的基本原理没有发生改变,但样品的测试无疑经历了重大的变化。测试控制方式和疲劳试验数据的研究分析正逐步实现数字化,这是疲劳测试发展进程中发生的最大变化。
一个非常重要的发展正在行业中获得人们的注意力——“即时”制造方法的日益普及,促使着制造商们考虑如何有效减少疲劳测试阶段所需的时间。一般情况下,较长的测试周期需要特定的时间框架,如果加速疲劳测试频率则会对样品测试过程中的温度产生影响,进而改变测试条件和测试结果。
在业内,疲劳测试的最终目标是将超高周疲劳测试引入到当前的低周疲劳/高周疲劳测试中,这将有助于更加精准的预测汽车行业内汽车产品的长期疲劳寿命。
另一个重大的变化在于我们正致力于材料疲劳测试的建模研究。模型预测将被引入到虚拟铸造和测试流程中,这是行业内的一个重大改变。这些虚拟过程将代替当前所用的加工和测试方法,进而节省大量的经济成本,因为据我所知,材料的加工和测试需要一笔不小的花费。
材料及产品的使用寿命预测是一个很大的研究领域,这些测试研究使得制造商们能够快速对其制造工艺和材料进行改变及优化从而提高汽车产品的使用性能。
如今,一些新型的加工制造技术,例如3D打印技术,又将带来新的机遇和挑战。在现阶段,我们不能精确的预测一些材料在大范围内抗疲劳性能,但随着我们收集到更多有关于制造技术和材料性能的信息,我们将看的更清楚。
JOHNSON: 各种各样的复合材料的应用将会是汽车行业未来发展的关键,这意味着一些参考标准以及理论知识需要得到改进和完善。
今天,汽车制造商迫切需要减少汽车尾气排放,这也是最终的商业驱动因素之一,虽然许多高新技术可以用于提高汽车传动系效率以实现这一目标,但是通过降低车身的总体质量则是一种更简单有效的办法。正如前面所说,这可以通过在汽车上某些部位采用碳纤维增强复合材料以及其它一些类似的轻质材料实现。
PANTER: 随着高强度钢和合金材料的进一步开发、3D打印技术的持续发展进步、新型复合材料以及组装技术的发展(包括紧固件和粘结工艺的进步等),我们需要确保当前以及未来的疲劳测试能够跟上技术的需求。 计算机建模方面的进步能够为组件和子系统的测试程序提供更精确的加载参数。非接触、实时(虚拟)应力应变测量体系的发展同样能够帮助人们更好的了解载荷加载路径,并且开发出新的疲劳测试程序。