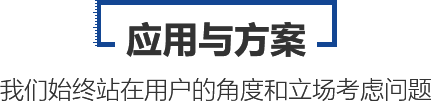
塑料应用领域非常广泛,不同的应用领域所需要的性能也不完全一样,下面介绍一下塑料的力学性能测试以及影响因素。
2、弯曲性能
3、压缩性能
4、冲击性能
5、硬度试验
6、其他力学性能测试
1、拉伸性能测试
定义:
在规定的试验温度、湿度及拉伸速度下,通过对塑料试样的纵轴方向施加拉伸载荷,使试样产生形变直至材料破坏。记录下试样破坏时的负荷和对应的标线间距离的变化等情况,可绘制出应力-应变曲线。
影响因素:
(1)试样的制备与处理
拉伸试验要求做成哑铃形试样;
制样方式有两种:一是用原材料制样;二是从制品上直接取样。
用原材料制成试样有几种方法,包括模压成型、注塑成型、压延成型或吹膜成型等;
不同方法制样的试验结果不具备可比性;
同一种制样方法,要求工艺参数和工艺过程也要相同;
试样制备好后,要按GB/T 2918-1998标准,在恒温恒湿条件下放置处理。
(2)材料试验机
影响因素主要有:测力传感器精度、速度控制精度、夹具、同轴度和数据采集频率等。
测力传感器一般要求传感器的精度在0.5%以内。
拉伸速度要求平稳均匀,速度偏高或偏低都会影响拉伸结果。
试验机的同轴度不好,拉伸位移将偏大,拉伸强度有时将受到影响,结果偏小。
(3)试验环境
影响塑料拉伸试验结果的因素主要是温度和湿度。GB/T 2918-1998,标准实验室环境温度为(23±2)℃,相对湿度为45%~55%。
(4)操作过程
一般情况下,拉伸速度快,屈服应力和拉伸强度变大,而断裂伸长率将减小。
高速拉伸时,分子链段的运动跟不上外力作用的速度,塑料呈现脆性行为,表现为拉伸强度变大,断裂伸长率减小。
(5)数据处理
现在的材料试验机多数由计算机控制,数据处理已程序化,但是有些数据还是依靠人为测试和计算的,如试样尺寸、位移变化、伸长率计算及脱机试验等。
测定塑料弯曲性能采用的一种方法是三点负载体系,二种方法是四点负载体系。
影响因素:
(1)跨厚比
选择跨厚比时需综合考虑剪力、支座水平推力以及压头压痕等综合影响因素。
(2)应变速率
在相同的试验厚度下,跨度越大则应变速率越小;试验速度越大则应变速率越大。
(3)加载压头圆弧和支座圆弧半径
加载压头圆弧半径过小,造成压头与试样质检不是线接触,而是面接触;若压头半径过大,对于大跨度就会增加剪力的影响,容易产生剪切断裂。
(4)温度
弯曲强度都随着温度升高而下降,但下降程度各有不同。
(5)操作影响
试样尺寸的测量、试样跨度的调整、压头与试样的线接触和垂直状况以及挠度值零点的调整。
压缩性能是描述材料在较低的压缩负载和均匀加载速率下的行为。
压缩性能包括弹性模量、屈服应力、屈服点以外的形变、压缩强度、压缩应变和细长比。
在实际应用中,压缩负载并不总是瞬间加上的,因此,不考虑塑料的刚度和强度对时间依赖性的标准试验结果,就不能作为设计零件的基础。
试验是把试样置于试验机的两压板之间,并在沿试样两个端部表面的主轴方向,以恒定速率施加一个可以测量的大小相等而方向相反的力,使试样沿轴方向缩短,而径向方向变大,产生压缩形变,直至试样破裂,屈服或试样变形达到一预先规定的数为止。
影响因素:
(1)试样材料:
例如材料内应力分布、材料结构、试样的成型加工方式等;
(2)试验条件:
例如试样形状、试样尺寸、试验机的上下压板的表面粗糙度或摩擦力以及试验速度等。
冲击试验是用来评价材料在高速载荷状态下的韧性或对断裂的抵抗能力的试验。
塑料材料的冲击强度在工程应用上是一项重要的性能指标,它反映不同材料抵抗高速冲击而致破坏的能力。
冲击试验可分为摆锤式(包括简支梁和悬臂梁式)、落球(落锤)式和高速拉伸冲击试验等。
不同材料、不同用途制品可选择不同的试验方法。
摆锤式冲击试验包括简支梁型和悬臂梁型。
这两种方法都是将试样放在冲击机上规定位置,然后使摆锤自由落下,使试样受到冲击弯曲力而断裂,试样断裂时单位面积或单位宽度所消耗的冲击功即冲击强度。
简支梁冲击试验是摆锤打击简支梁试验;悬臂梁则是用摆锤打击有缺口的悬臂梁的自由端。
影响因素:
(1)试样制备
每种制样过程都要符合相关标准,不同制样方法不具有可比性。
(2)样尺寸
规格要一致。不同加工方式加工的试样,其测值不具可比性。
(3)试验环境
冲击强度值均随温度的降低而降低。湿度对某些塑料冲击强度有影响。
(4)操作过程
如冲击速度,冲击摆锤刀口与试样打击面吻合。简支梁冲击试验中,如果试样与支架没有贴紧,则容易产生多次冲击使测试结果不准确。
(5)数据处理
数据处理与试验结果的准确度有着密切关系。
测定硬度的方法主要有三种类型:
(1)测定材料耐顶针压入能力的试验,如邵氏硬度(肖式硬度)、球压痕硬度试验等;
(2)测定材料对尖头或其它材料的耐划痕硬度试验,如莫氏硬度(Mobs)等;
(3)测定材料回弹性的硬度试验,如洛氏硬度,邵氏反弹硬度试验等。
邵氏A型适用于软质塑料及橡胶;邵氏C型和邵氏D型适用于较硬或硬质塑料和硫化橡胶。
球压痕硬度实验适用于柔软的弹性体到较硬的塑料。
洛氏硬度实验主要用于刚硬的工程塑料的硬度评价。
将规定形状的压针,在标准的弹簧压力下和规定的时间内,把压针压入试样的深度转换为硬度值,表示该试样材料的邵氏硬度等级。
影响因素:
(1)试样厚度:试样过薄,将使测定的硬度值偏大。
(2)压针:压针端部形状越平坦,测得的硬度值越大。
(3)温度:测试温度高,测得的硬度值低。
(4)读数时间:随读数时间的增加而下降。
(5)测点间距离
属于静载压痕法硬度试验,可用于软的弹性体材料到较刚硬塑料的硬度值评价。
影响因素:
(1)试验仪器的影响
(2)测试温度的影响
(3)试样厚度的影响
(4)主试验力保持时间的影响
(5)读数时间的影响
(1)剪切试验
剪切强度定义为在剪切应力作用下,使试样移动部分与静止部分呈完全脱离状态所需之负荷。
影响因素:a:剪切速度:同一种材料随着剪切试验速度的增加,其剪切强度也变大。b:试样厚度:材料在制造过程中,不可避免地会产生一些气孔杂质或低 分子物质等缺陷,试样越厚,存在缺陷的概率也越高,因此一般试样越厚其剪切强度值也越低。c:环境温度:随着温度的升高,剪切强度明显下降,且热塑性材料 较热固性材料的影响更为明显。
(2)蠕变及应力松弛试验
蠕变试验:试验样品使用相关材料标准或GB/T 1040.2-2006中规定的测定拉伸性能的试样。
应力松弛试验:在恒定形变下,物体的应力随时间而逐渐衰减的现象称为应力松弛;应力松弛是一种理论上类似于蠕变特点的松弛行为,塑料应力松弛程度依赖于应变、时间和温度条件。
影响因素:
a温度的影响:温度越高,蠕变值和应力松弛值也越大。
b压力的影响:变大压力,降低分子链段的活动性,即降低了柔量。
c聚合物分子量的影响:分子量较小,熔融粘度与分子量成正比。
d交联状态的影响:交联度提高,蠕变速率明显下降。
e共聚和增塑作用的影响:共聚和增塑使蠕变和应力松弛曲线在温度轴方向产生平移。
f结晶化的影响:结晶能大大减少蠕变或应力松弛。
g聚合物分子结构的影响:分子链愈柔曲,蠕变和应力松弛就愈明显;相反,刚性分子链及链间作用力大的材料,蠕变及应力松弛就小。
(3)疲劳试验
疲劳是在较静态极限载荷小的载荷作用下,经过一定的时间周期后,首先在材料中产生很小的疲劳裂纹,然后在裂纹或材料的缺陷处(如杂质、填料、气泡、裂 隙、表面擦伤、刻痕等)处产生应力集中,使此处的应力比其他地方高数倍,数十倍或数百倍,就使裂纹迅速扩展,而导致材料的力学性能减弱或破坏。
疲劳是材料在周期性的交变载荷作用下发生的破坏。
银纹化和剪切流变是聚合物疲劳过程中普遍的分子链变形方式。
(4)摩擦及磨耗性能
摩擦性能:指在摩擦过程中,材料的表面不断损失的性能。
影响因素:
a) 温度对摩擦系数有一定的影响,但都不太大。
b) 塑料摩擦系数随负荷变大而缓慢下降。
c) 在中、低速度范围内,塑料的摩擦系数随速度的增加而变大,但在高速下,随速度的增加而降低。
d) 配对材料 同一种塑料,因对磨材料的不同,其摩擦系数有很大差别。
e) 表面的粗糙度 接触表面愈粗糙,摩擦系数愈大。但聚四氟乙烯-钢的摩擦系数,当钢的光洁度很高时,却反而变大,只有当钢的光洁度在适当范围内才降到较小,这可能和聚四氟乙烯在钢表面的粘附有关。
f) 其他因素:如塑料的加工方法,试样的厚度等。
磨耗性能:在摩擦力作用下的整个过程中,发生一系列的机械、物理、化学的相互作用,以致材料表面发生尺寸变化和物质损耗。
影响因素:
a) 砂轮 砂轮是试验时的磨料,其切割力的大小,直接影响试验结果,在使用过程中,随着时间的延长,在其表面会附着一层发粘的胶沫,甚至染上油污,这些对试验结果都有影响。
b) 角度 角度变大,其滑动率也随之变大,磨耗量呈直线激烈增加。
c) 负荷 磨耗量随负荷的增加而逐渐变大。
d) 试样 试样长度越短磨耗量越大,试样越长磨耗量越小;试样厚度增加,磨耗量逐渐变大;试样夹板的大小,试样打滑的情况对磨耗量都有影响;转速的影响不太明显。
声明:文章旨在传播应用知识,内容和图片来源于网络,如涉版权问题请与我公司联系,我们会快速度处理。
无锡东立智能技术有限公司
电话:0510-82400646
我们始终站在用户的角度和立场考虑问题,与用户互动式交流,为用户提供详尽的仪器用途、重要参数的说明,还为客户提供不同品牌产品间的性能比较,给用户最中肯的购买建议。