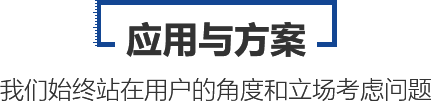
超薄切片机需要使用玻璃刀,为电镜和光镜提供超薄样本切片。
对于树脂切片和冷冻切片(Tokuyasu样本)的玻璃刀,其刀锋非常锋利、坚固、稳定。采用断裂法制备好的玻璃刀时,玻璃条的质量非常重要。玻璃条由精选玻璃生产而成,厚度和质量均经过准确把控。只有采用高质量标准来严格把控公差,才能从一块玻璃中制出两把好的玻璃刀。
图1:成刀
平衡断裂概念
在科学级质量的玻璃条中制造受控的笔直断裂,要求制刀机在划痕的两侧施加相同的重量和压力。此外,从底部接触玻璃的支撑元件尽可能减小表面接触,以免在断裂之前对玻璃施加非受控的压力。
采用平衡断裂法(图2)制刀时,一根玻璃条会从中间划痕处断裂成相等的两半。划痕两侧的玻璃重量相等,断裂是平衡的,新产生的断裂面是平整的。不断将新产生的玻璃条断成相等的两半,可以得到一定数量的方形玻璃板。
所有方形玻璃板都拥有平直的侧边以及准确的直角,而连续断裂法得到的方形玻璃板的表面常常会弯曲变形。
图2:平衡断裂法
划痕和断裂原理
制作高质量玻璃刀通常需要制作出一批相等的方形玻璃板,在玻璃上准确地划出划痕,准确地施加压力,使其断裂。
通常情况下,当断裂发生在靠近拐角的地方(长划痕)时,刀锋更加平直,对面刀肩更窄。过去建议使用短划痕制作冷冻超薄切片,因为这样一来自由断裂的时间较长,可以制得锋利、较长的可用刀锋[1, 2]。
每个划痕已经预设好,划痕距离方块两个角的距离相等。断裂发生时,玻璃下方垫着两枚不锈钢半球,上方则由两枚断裂销固定。这种断裂可以让划痕向其两侧尽可能地延伸,直至自由断裂发生。自由断裂的方向由断裂两侧玻璃的重量以及两侧施加的力决定。
自由断裂向方形玻璃板的边缘弯曲,制得一把刀,且刀锋对面出现平边(刀肩)(图3a)。若划痕沿着方块的中心延伸,则产生的刀肩会非常窄,此时刀的角度更加接近45°(图3b)。
这是冷冻超薄切片的优选设置。进行树脂切片时,则可以将刀肩设置得稍微大一些(~0.5 mm),产生更大的刀角度,这样能更加稳定。
图3a
图3b
玻璃刀真实刀角度
在方形玻璃板上划出划痕时,所有划痕距离方形玻璃板直角还有一定距离。对划痕两侧施加压力,断裂开始,首先可以看到划痕开始变深。断裂沿着划痕向方形玻璃板两角延伸。划痕到达两个角后,自由断裂开始。断裂沿着划痕延伸,到达两角时向方形玻璃板的一边偏离弯曲。因此,玻璃刀的真实刀角会略大于划痕角度。
玻璃刀的真实角度会随着划痕偏离对角线角度的变大而变大。这种情况下,刀肩就会变宽。
例如,用方形玻璃板制作玻璃刀时,若刀肩较小(<0.5 mm),则真实刀角度会接近45°。刀肩变大(>0.5 mm)后,会进一步放大真实刀角度,甚至可能使其大于55°(图4)。
图4
可用刀锋长度
在暗场照明下用体式镜来检查玻璃刀刀锋(或用超薄切片机并使用背光灯照明),可以看出刀锋的中间部分用来做超薄切片。刀锋右侧有可见的毛刺(锯齿状),会使刀的质量下降。受应力线影响,刀锋左侧也不适合做切片(图5)。
从应力线离开刀锋到刀锋出现毛刺(锯齿状),这一段刀锋可用做超薄切片。
注 意
1、使用8 mm玻璃条比使用6.4 mm玻璃条多30%可用刀锋长度!
2、方形玻璃板断裂成玻璃刀时,施加的力越小,应力线就会越快离开刀锋,锯齿状毛刺也更少。这样一来,可用刀锋长度就会更长。
检查刀锋
制得一对玻璃刀后,可以在超薄切片机上检查刀锋质量。
使用背光灯照明,将间隙角设置为较大值,可以看见一道非常细的白线(图6)。这条线可用于判断刀锋的质量,白线平直、无尘、无油渍、无指纹、无玻璃毛刺。
另外,也可以使用顶灯照明观察玻璃刀的刀锋质量(图7)。
图8所示玻璃刀质量不合格,不能使用。抓取玻璃刀时,指纹留在了刀锋上。
图9(顶部)展示了一对玻璃刀,它们在断裂后并排放置。图中(图9底部)还展示了两把玻璃刀的刀肩细节。在断裂过程中,右侧刀锋与左侧刀肩对应,左侧刀锋与右侧刀肩对应。
图6
图7
图8
参考资料:
1. Griffiths G, Simons K, Warren G and Tokuyasu KT: Immunoelectron microscopy using thin, frozen sections: Application to studies of the intracellular transport of Semliki Forest virus spike glycoproteins. In: Methods in Enzymology 466–485 (1983).
2. Tokuyasu KT: Application of cryoultramicrotomy to immunocytochemistry. Journal of Microscopy 143 (2): 139–149 (1986).